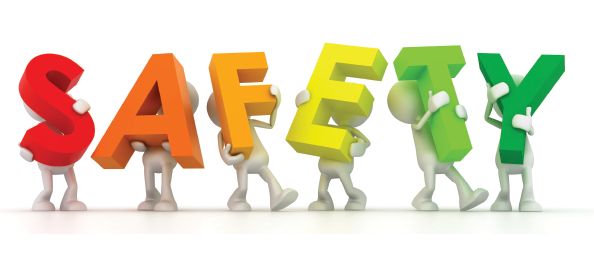
Newly revised guidelines by OSHA encourage employers to implement workplace plans and to take a proactive approach to finding and fixing hazards before they cause injury, illness or death. OSHA is encouraging comments on the updated Safety and Health Program Management Guidelines through February 15, 2016. Safety.BLR.com, Emily Clark, points out the key elements.
OSHA recently released a draft updated version of its voluntary Safety and Health Program Management guidelines and is seeking public comment on the revisions. Keep reading to find out what’s new—and what it could mean for employers.
According to OSHA, the new guidelines build on the previous version, which was published in 1989, and incorporate lessons learned from successful approaches and best practices under the agency’s Voluntary Protection Program (VPP) and Safety and Health Achievement Recognition Program (SHARP). Principles from industry and international consensus standards such as ANSI Z10 and OHSAS 18001 also inform the guidance.
Key new elements of the guidelines include:
- A proactive approach to finding and fixing hazards before they cause injury, illness, or death;
- Improved safety and health information for all types of workplaces;
- Help for small and medium-sized businesses;
- An increased emphasis on worker involvement; and
- Strategies for better communication and coordination on multiemployer worksites.
Essentials of a safety and health management program
OSHA’s guidelines identify seven core elements of a safety and health management program
- Management leadership. Management shows a commitment to safety as a core organizational value, provides adequate resources and support for safety efforts, and communicates that commitment both formally and by example.
- Worker participation. Workers are involved in all aspects of the safety program, are encouraged to communicate safety concerns, and understand their roles and responsibilities for safety.
- Hazard identification and assessment. Procedures to continually identify workplace hazards and evaluate risks are in place and are effectively implemented.
- Hazard prevention and control. Employers and workers cooperate to eliminate, prevent, and control workplace hazards, and the effectiveness of hazard controls is verified.
- Education and training. All workers are trained on the safety and health management program and their responsibilities under the program, and all workers are trained to recognize hazards and follow safe work practices and hazard controls.
- Program evaluation and improvement. Control measures are periodically evaluated for effectiveness, and processes are established to monitor program effectiveness and opportunities for improvement.
- Coordination and communication on multiemployer worksites. Host employers and all contract employers coordinate on matters related to safety and health, and all workers are informed of the hazards they could be exposed to at a worksite.
Impact for employers
Although the guidelines are purely voluntary, OSHA Administrator David Michaels has on several occasions expressed that he would support a regulation requiring all businesses to implement injury and illness prevention programs (IIPPs).
The IIPP initiative is currently in the “long-term action” phase, indicating that rulemaking is unlikely to take place in the near future. However, the abstract describing the IIPP effort in OSHA’s regulatory agenda is identical to some of the introductory language to the new voluntary guidelines, perhaps indicating that the new guidelines constitute OSHA’s effort to persuade employers to adopt IIPPs without a formal regulatory requirement.
Some states, including California and Washington, do require employers to develop IIPPs or similar safety management programs, and others offer workers’ compensation discounts as an incentive to do so.
Members of the public have until February 15, 2016, to submit comments on the proposed guidelines. OSHA provides information on the type of feedback it is seeking at https://www.osha.gov/shpmguidelines/SHPM_questions.html, and comments can be submitted at http://www.regulations.gov/#!docketDetail;D=OSHA-2015-0018.